




FRP tower
Weight
- 产品描述
-
- Commodity name: FRP tower
Fiberglass towers (desulfurization towers, absorption towers, purification towers, washing towers, drying towers, etc.) are mainly used in flue gas desulfurization and denitrification treatment systems in power plants due to their advantages of high temperature resistance, corrosion resistance, wear resistance, and long service life. Metallurgy, petrochemicals, electronics, medicine, textiles and other environmental protection fields protect the environment, save energy and create value.
Fiberglass towers (desulfurization towers, absorption towers, purification towers, washing towers, drying towers, etc.) are mainly used in flue gas desulfurization and denitrification treatment systems in power plants due to their advantages of high temperature resistance, corrosion resistance, wear resistance, and long service life. Metallurgy, petrochemicals, electronics, medicine, textiles and other environmental protection fields protect the environment, save energy and create value.
The fiberglass tower adopts a microcomputer-controlled horizontal fiber winding process. That is, under the control of a microcomputer, the mold rotates around the axis, and the filament winding head carries the resin-impregnated glass fiber to reciprocate along the axis of the mold. The speed ratio of the two movements is controlled by the microcomputer. The number of winding layers is controlled by a microcomputer according to pre-entered parameters. After the resin is cured, the product is formed on the surface of the mold.
1. Technical characteristics of horizontal winding molding process: During the molding process, the mold is parallel to the ground, so it is called horizontal winding. The maximum diameter can reach 15 meters and the length is 20 meters. It has four advantages:
1. Integral molding: The barrel is wound as a whole (including the head), with no structural layer joints. The axial and circumferential forces of the barrel are reasonably and evenly distributed, with good overall performance, high strength, no stress concentration areas, and long service life;
2. Uniform resin content: During the winding process, the equipment is placed horizontally and rotates continuously, so there will be no resin dripping or uneven resin content;
3. Reasonable structure: It adopts steel mold and the inner lining is injection molded. It has high resin content, smooth inner surface and no capillary phenomenon. The structural layer is formed by spiral circumferential cross-winding, with a resin content of 35±5%. The outer protective layer is smooth and uniform in color;
4. The head has strong load-bearing capacity: the cylinder body and the head are reinforced as a whole to form a bud-type coating. The head has a large capacity to resist wind load, snow load and operating load.
2. Implementation standards: HG/T20696-1999 "Design Regulations for FRP Chemical Equipment"
Previous Page
Next Page
Related Products
online message
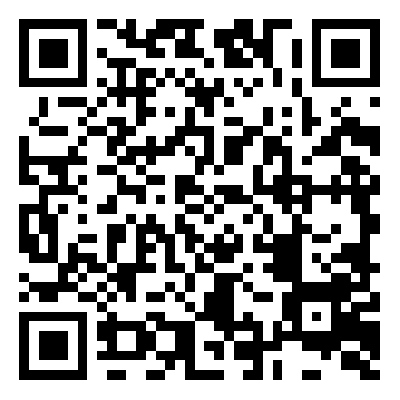
WeChat Public Number
Nanjing Xinhe Composites Co.,Ltd.
Address: KAIPING RD ,DONGPING HI-TECH DEVELOPMENT ZONE,NANJING,JIANGSU,CHINA,211212
Fax: 025-57493228
Tel: 025-57492608
Email: admin@nnfrp.com
copyright©2023 Nanjing Xinhe Composites Co.,Ltd.
Website Construction: www.300.cn nanjing |SEO Tags